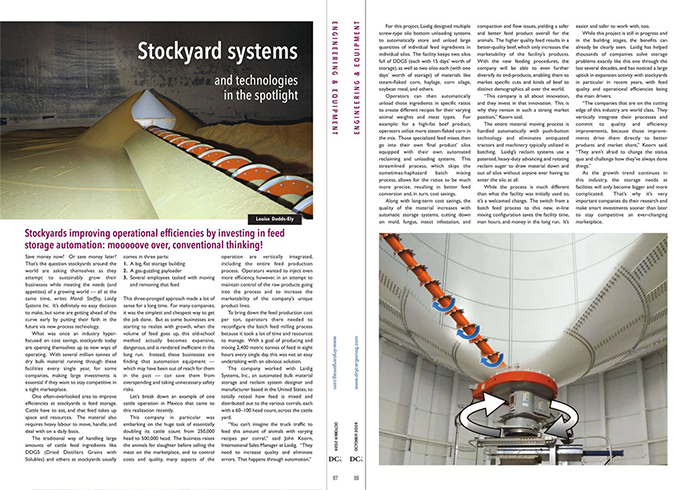
As Seen in Dry Cargo International Magazine: "Stockyards improving operational efficiencies by investing in feed storage automation: mooooove over, conventional thinking!"
Stockyards improving operational efficiencies by investing in feed storage automation
Mooooove over, conventional thinking!
Save money now? Or save money later? That’s the question stockyards around the world are asking themselves as they attempt to sustainably grow their businesses while meeting the needs (and appetites) of a growing world—all at the same time. It’s definitely no easy decision to make, but some are getting ahead of the curve early by putting their faith in the future via new process technology.
What was once an industry hyper-focused on cost savings, stockyards today are opening themselves up to new ways of operating. With several million tons of dry bulk material running through these facilities every single year, for some companies, making large investments is essential if they want to stay competitive in a tight marketplace.
One often-overlooked area to improve efficiencies at stockyards is feed storage. Cattle have to eat, and that feed takes up space and resources. The material also requires heavy labor to move, handle, and deal with on a daily basis.
The traditional way of handling large amounts of cattle feed ingredients like DDGS (Dried Distillers Grains with Solubles) and others at stockyards usually comes in three parts:
- A big, flat storage building
- A gas-guzzling payloader
- Several employees tasked with moving and removing that feed
This three-pronged approach made a lot of sense for a long time. For many companies, it was the simplest and cheapest way to get the job done. But as some businesses are starting to realize with growth, when the volume of feed goes up, this old-school method actually becomes expensive, dangerous, and is rendered inefficient in the long run. Instead, these businesses are finding that automation equipment—which may have been out of reach for them in the past—can save them from overspending and taking unnecessary safety risks.
Let’s break down an example of one cattle operation in Mexico that came to this realization recently:
This company in particular was embarking on the huge task of essentially doubling its cattle count from 250,000 head to 500,000 head. The business raises the animals for slaughter before selling the meat on the marketplace, and to control costs and quality, many aspects of the operation are vertically integrated, including the entire feed production process. Operators wanted to inject even more efficiency, however, in an attempt to maintain control of the raw products going into the process and to increase the marketability of the company’s unique product lines.
To bring down the feed production cost per ton, operators there needed to reconfigure the batch feed milling process because it took a lot of time and resources to manage. With a goal of producing and mixing 2,400 MT of feed in eight hours every single day, this was not an easy undertaking with an obvious solution.
The company worked with Laidig Systems, Inc., an automated bulk material storage and reclaim system designer and manufacturer based in the United States, to totally retool how feed is mixed and distributed out to the various corrals, each with a 60-100 head count, across the cattle yard.
“You can’t imagine the truck traffic to feed this amount of animals with varying recipes per corral,” said John Koorn, International Sales Manager at Laidig. “They need to increase quality and eliminate errors. That happens through automation.”
For this project, Laidig designed multiple screw-type silo bottom unloading systems to automatically store and unload large quantities of individual feed ingredients in individual silos. The facility keeps two silos full of DDGS (each with 15 days’ worth of storage), as well as two silos each (with one days’ worth of storage) of materials like steam-flaked corn, haylage, corn silage, soybean meal, and others.
Operators can then automatically unload those ingredients in specific ratios to create different recipes for their varying animal weights and meat types. For example: for a high-fat beef product, operators utilize more steam-flaked corn in the mix. Those specialized feed mixes then go into their own “final product” silos equipped with their own automated reclaiming and unloading systems. This streamlined process, which skips the sometimes-haphazard batch mixing process, allows for the ratios to be much more precise, resulting in better feed conversion and, in turn, cost savings.
Along with long-term cost savings, the quality of the material increases with automatic storage systems, cutting down on mold, fungus, insect infestation, and compaction and flow issues, yielding a safer and better feed product overall for the animals. The higher quality feed results in a better-quality beef, which only increases the marketability of the facility’s products. With the new feeding procedures, the company will be able to even further diversify its end-products, enabling them to market specific cuts and kinds of beef to distinct demographics all over the world.
“This company is all about innovation, and they invest in that innovation. This is why they remain in such a strong market position,” Koorn said.
The entire material moving process is handled automatically with push-button technology and eliminates antiquated tractors and machinery typically utilized in batching. Laidig’s reclaim systems use a patented, heavy-duty advancing and rotating reclaim auger to draw material down and out of silos without anyone ever having to enter the silo at all.
While the process is much different than what the facility was initially used to, it’s a welcomed change. The switch from a batch feed process to this new, in-line mixing configuration saves the facility time, man hours, and money in the long run. It’s easier and safer to work with, too.
While this project is still in progress and in the building stages, the benefits can already be clearly seen. Laidig has helped thousands of companies solve storage problems exactly like this one through the last several decades, and has noticed a large uptick in expansion activity with stockyards in particular in recent years, with feed quality and operational efficiencies being the main drivers.
“The companies that are on the cutting edge of this industry are world class. They vertically integrate their processes and commit to quality and efficiency improvements, because those improvements drive them directly to better products and market share,” Koorn said. “They aren’t afraid to change the status quo and challenge how they’ve always done things.”
As the growth trend continues in this industry, the storage needs at facilities will only become bigger and more complicated. That’s why it’s very important companies do their research and make smart investments sooner than later to stay competitive an ever-changing marketplace.
+1 (574) 256-0204
Fax: (574) 256-5575
Business hours: 7 a.m.–4:30 p.m. (EST), Monday–Friday